Polypropylene yarn, often called PP yarn, is a real workhorse in the textile world. If you’re in the business of creating durable fabrics, strong ropes, comfortable upholstery, or even specialized garment components, chances are you’ve come across this unique synthetic fiber. But what makes polypropylene stand out? As Allen, representing a dedicated manufacturer and supplier in China, I’ve seen firsthand how understanding the specific features of polypropylene yarn, its tenacity, and its wide range of applications can significantly impact your final product quality and bottom line. This article dives deep into the world of polypropylene yarn, exploring everything from its basic properties to its manufacturing nuances and diverse uses. Whether you’re a seasoned procurement officer like Mark Thompson, exploring cost-effective sourcing options, or a designer seeking the right material for your next project, understanding PP yarn is crucial. We’ll cover its strengths, limitations, how it compares to other fibers like polyester, and what to look for when sourcing it, ensuring you make informed decisions for your business.
What Exactly is Polypropylene Yarn (PP Yarn)?
At its core, polypropylene yarn is a type of textile yarn spun from polypropylene, a synthetic polymer. You might hear it referred to simply as PP yarn. This material belongs to the polyolefin group and is derived from propylene gas, a byproduct of petroleum refining. What makes it interesting from a materials science perspective is that it’s a thermoplastic, meaning it can be melted and reformed, which is key to its production process. The specific type used for fibers is typically isotactic polypropylene, which provides the right structure for creating strong, usable yarn.
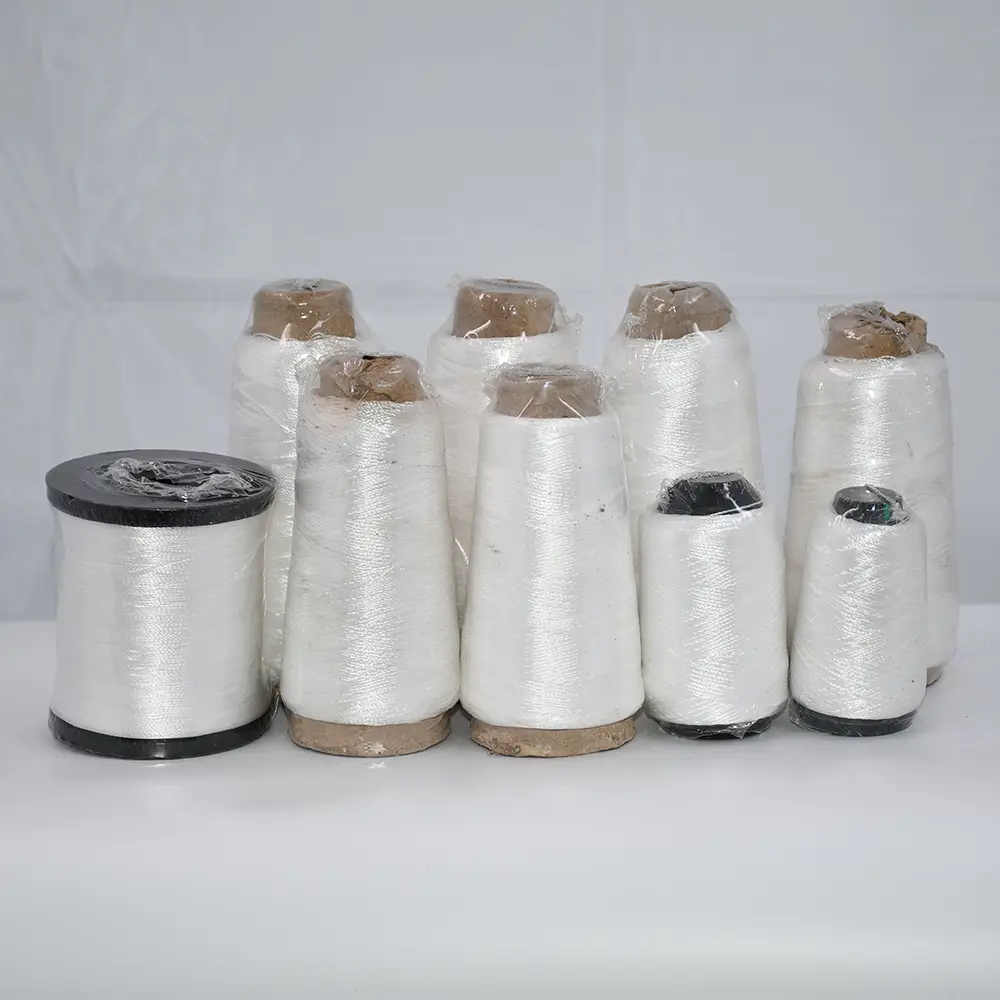
One of the first things people notice about polypropylene yarn is its incredibly low weight. In fact, it holds the title for the lightest commercial synthetic fiber available! Its density is lower than water, meaning it actually floats. This characteristic alone opens up many possibilities for lightweight fabric and products where weight is a critical factor. Unlike natural fibers or even some other synthetics, polypropylene doesn’t absorb much moisture, which we’ll discuss more later. It’s a robust fiber known for its durability and resistance, making it a popular choice across various industries. Think of it as a versatile building block for countless textile products.
This yarn is essentially long, continuous strands made from polypropylene fibers. These strands can vary greatly in thickness (denier) and can be processed in different ways – smooth filament yarn, textured yarn, or even fibrillated yarn (where the film is stretched and split to create a net-like structure). This versatility in form allows manufacturers like us to tailor the PP yarn precisely to the end-use application, whether it’s for weaving into strong industrial fabric or knitting into comfortable sportswear. It’s a synthetic marvel that offers a unique combination of properties.
How is Polypropylene Yarn Made?
Creating polypropylene yarn involves a fascinating process that transforms tiny polymer pellets into strong, continuous filaments. It starts with polypropylene resin, typically in the form of small beads or pellets. These pellets are melted down in an extruder, essentially a large heated screw that pushes the molten polymer forward. It’s crucial at this stage to maintain precise temperature control to ensure the polypropylene melts uniformly without degrading. As manufacturers, we pay close attention to the quality of the raw resin and the extrusion parameters, as this directly impacts the final yarn quality.
Once molten, the polypropylene is forced through a spinneret – a metal plate with many tiny holes. As the polymer streams emerge from these holes, they begin to cool and solidify, forming continuous filaments. The size and shape of the spinneret holes determine the initial thickness and cross-sectional shape of the fiber. These freshly formed filaments are then drawn or stretched. This drawing process is critical; it aligns the polymer molecules along the length of the fiber, significantly increasing its strength and wear resistance, or tenacity. The degree of drawing determines whether we produce standard tenacity or high tenacity yarn.
After drawing, the filaments can be processed further. They might be textured to add bulk and softness for applications like upholstery or apparel, or wound directly onto bobbins as smooth filament yarn. For fibrillated yarn, a slightly different process involves extruding a film, stretching it, and then mechanically splitting it to create a coarse, strong yarn often used for rope and industrial fabric. Throughout this industrial production, quality checks are paramount – monitoring filament consistency, tenacity, elongation, and shrinkage to ensure the PP yarn meets the required specifications for demanding applications, from intricate textile weaves to robust geotextiles. The entire process is highly efficient and suitable for mass production.
What are the Standout Features of Polypropylene Yarn?
Polypropylene yarn boasts a unique set of characteristics that make it highly desirable for specific applications. Perhaps its most defining feature is its low density. As mentioned, it’s the lightest of all commercial textile fibers, weighing even less than water. This translates directly into lighter fabrics and end products, which is a significant advantage in areas like sportswear, luggage, and automotive components. Imagine a rope that floats or a garment that feels incredibly light – that’s the power of polypropylene.
Another major advantage is its extremely low moisture absorption. Polypropylene fiber is hydrophobic, meaning it actively repels water rather than absorbing it. This low moisture characteristic leads to several benefits: fabrics made of polypropylene dry very quickly, they don’t feel clammy against the skin (making them great for activewear), and they are highly resistant to staining from water-based substances. This resistance extends to dirt and stains in general, making polypropylene fabric easy to clean and maintain, ideal for carpets and upholstery. It also means the fiber retains its strength even when wet.
Furthermore, polypropylene yarn exhibits excellent chemical resistance. It stands up remarkably well against most acids and alkalis, solvents, and other chemicals. This makes it a top choice for industrial applications where exposure to harsh substances is common, such as filter fabrics, chemical storage containers (as liners), and geotextiles used in construction and environmental projects. Add to this its inherent resistance to mildew, mold, bacteria, and insects, and you have a yarn that offers exceptional high durability and longevity, particularly in challenging environments. It also possesses low thermal conductivity, offering good insulation properties, and is generally considered anti-allergic, making it used for medical purposes in certain non-woven fabrics.
Can Polypropylene Yarn Be Dyed Effectively?
This is a common question, and the answer requires a bit of nuance. Because polypropylene fiber is hydrophobic and has a crystalline structure that lacks active dye sites, it’s notoriously difficult to dye using conventional water-based dyeing methods used for fibers like cotton or even polyester. The dye molecules simply don’t penetrate or bond effectively with the polypropylene polymer. Trying to dye standard PP yarn often results in poor color uptake, uneven shades, and color that easily rubs off or fades.
However, this doesn’t mean you’re stuck with the natural off-white color of polypropylene! The industry solved this challenge long ago using a technique called dope dyeing or solution dyeing. In this process, concentrated color pigments are mixed directly into the molten polypropylene polymer before it’s extruded into fiber. The color becomes an integral part of the fiber itself, rather than just sitting on the surface. This method produces vibrant, deep colors that are exceptionally resistant to fading from washing, wear, abrasion, and even UV light exposure.
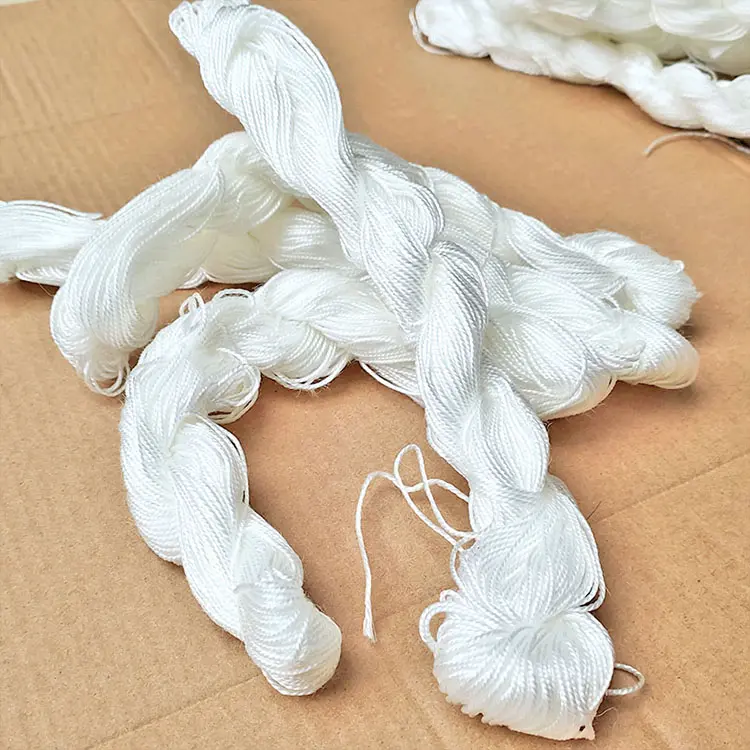
So, while you can’t easily dye finished polypropylene fabric or yarn yourself, manufacturers like us can provide high-quality dyed yarn in a vast array of colors through the dope dyeing process. When sourcing polypropylene yarn, if color is important, you should specifically look for solution-dyed yarn. This ensures excellent colorfastness and consistency, which is critical for products like upholstery, carpet, sportswear, and decorative items like yarn balls or curtain tassels. It eliminates the potential pain point of inconsistent dye lots that can sometimes occur with post-dyeing processes in other fibers.
Let’s Talk About Tenacity: How Strong is Polypropylene Yarn?
Tenacity is the textile term for the ultimate tensile strength of a fiber or yarn, usually measured in grams per denier (g/d). It essentially tells you how much pulling force a yarn can withstand before breaking, relative to its thickness. Polypropylene yarn offers good tenacity, making it a strong and reliable material for many applications. Standard polypropylene yarn typically has a tenacity ranging from 3.0 to 5.5 g/d. While this might not reach the absolute highest levels of some specialized industrial yarns, it provides excellent strength and wear resistance for its weight.
Where polypropylene truly shines is in its high tenacity variants. Through optimized manufacturing processes, particularly the drawing stage where the polymer molecules are highly aligned, we can produce high tenacity polypropylene yarn. This specialized yarn type can achieve tenacity values significantly higher than standard PP, often reaching 6.0 to 9.5 g/d or even more. This puts high tenacity PP yarn in competition with fibers like polyester for applications demanding high strength.
This impressive tenacity, combined with its light weight and chemical resistance, makes high tenacity polypropylene yarn ideal for demanding roles. Think about industrial slings, lifting straps, cargo nets, reinforcing materials in composites, high-performance ropes, and heavy-duty sewing threads like High Tenacity Polyester Filament Thread (though this link is for polyester, it demonstrates the type of high-strength application). The yarn is also inherently resistant to abrasion, further enhancing its durability in applications involving friction or rough handling. So, whether you need a standard yarn for general fabric or a high tenacity yarn for heavy-duty tasks, polypropylene offers effective solutions.
Where is Polypropylene Fabric Commonly Used?
The versatility of polypropylene yarn translates into an incredibly broad range of applications for polypropylene fabric. Its unique combination of properties – lightweight, strong, moisture-resistant, chemically inert, and often cost-effective – makes it a go-to material in numerous sectors. You’ll find polypropylene yarn used extensively in home furnishings, particularly in upholstery and carpet manufacturing. For carpets, it’s often used for the primary and secondary backing due to its strength, stability, and resistance to moisture and mildew. It’s also popular as a face fiber in carpets, especially loop pile (Berber) styles, because it’s durable, stain-resistant, and easy to clean.
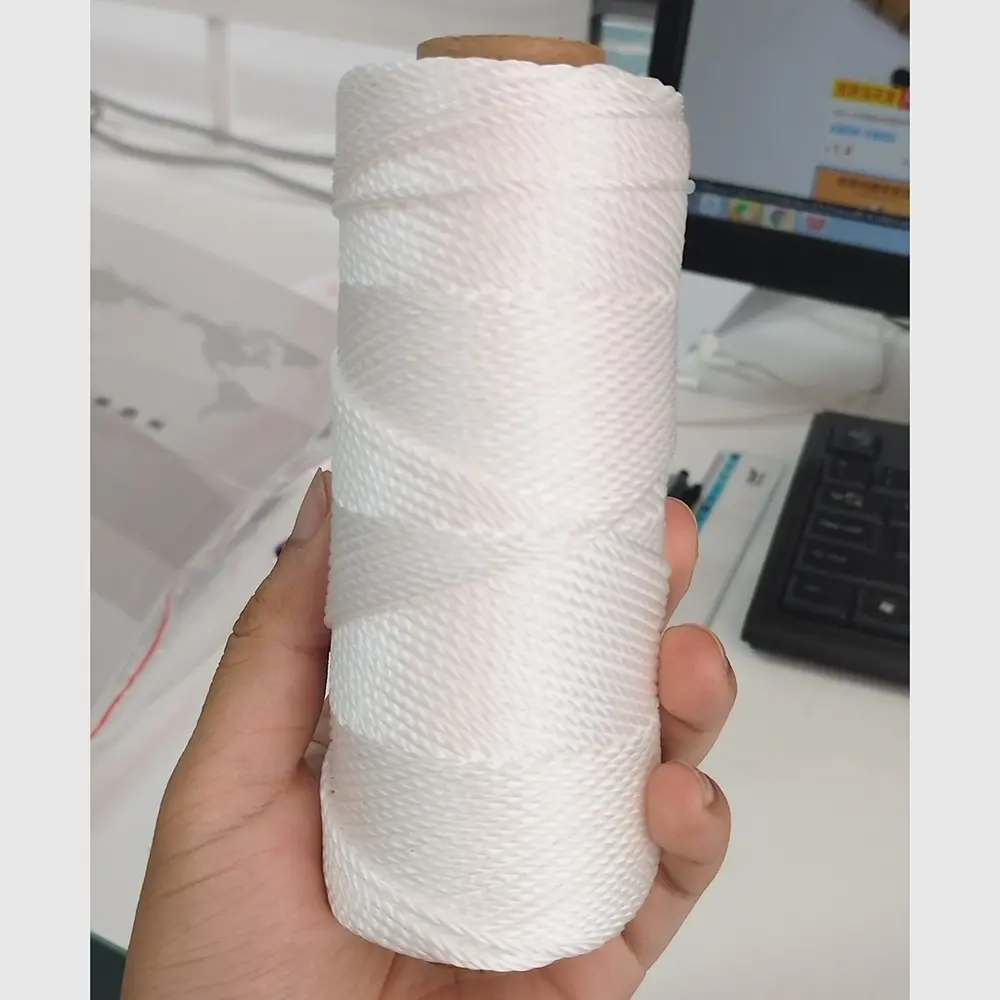
The automotive industry is another major consumer of polypropylene fabric. Its durability, light weight, and resistance to wear and tear make it suitable for car upholstery, interior trim, trunk liners, and floor mats. Beyond fabrics, PP yarn is fundamental in producing strong rope, twine, and net products used in fishing, agriculture, construction, and shipping. Think about sturdy packaging straps, baler twine, fishing nets, and safety nets – many of these rely on the tenacity and weather resistance of polypropylene. We offer various twines like Green Polyethylene Twited Twine, and while that’s polyethylene, similar principles apply to PP twine applications.
In the realm of technical textiles, polypropylene plays a vital role. Non-woven polypropylene fabrics are ubiquitous in hygiene products (diapers, sanitary pads), medical textiles (masks, gowns – leveraging its anti-allergic nature and barrier properties), and protective apparel. Woven polypropylene fabric is crucial in geotextiles for soil stabilization, drainage, and erosion control in civil engineering projects. Furthermore, its moisture-wicking properties make polypropylene yarn a component in performance sportswear and thermal underwear, helping to keep the wearer dry and comfortable. Its uses even extend to filter media, artificial turf, and bulk bags (FIBCs) for transporting powders and granules. This yarn is a versatile material indeed!
Is Polypropylene Yarn Suitable for Outdoor Applications?
Yes, polypropylene yarn is generally well-suited for many outdoor applications, primarily due to its inherent resistance to moisture, mildew, rot, and a wide range of chemicals. Since it absorbs virtually no water, polypropylene fabric won’t become heavy or weakened when wet, and it dries quickly. This makes it an excellent choice for products that are frequently exposed to rain, dew, or high humidity, such as outdoor furniture cushions, marine ropes, awnings, and covers.
Its chemical resistance also plays a role outdoors, protecting it from degradation caused by exposure to pollutants, acid rain, or cleaning agents. Unlike natural fibers, polypropylene won’t rot or support the growth of mold and mildew, ensuring longevity in damp conditions. This makes it ideal for items like sandbags, geotextiles buried in soil, and agricultural fabrics or net structures used for crop protection or shading. The strength and wear resistance also hold up well in many outdoor scenarios.
However, there’s one important consideration: standard polypropylene yarn has limited resistance to prolonged exposure to ultraviolet (UV) radiation from sunlight. UV damage can cause the fiber to degrade over time, becoming brittle and losing its strength and color. Fortunately, this weakness can be effectively addressed during manufacturing. By incorporating UV inhibitors and stabilizers into the polypropylene polymer before extrusion (often during the dope dyed process if color is also added), we can significantly enhance the yarn’s resistance to sunlight. When sourcing PP yarn or fabric specifically for long-term outdoor use, it’s crucial to specify the need for UV stabilization to ensure the product performs as expected and avoids premature degradation from UV damage.
Polypropylene Yarn vs. Other Synthetic Fibers: What’s the Difference?
Choosing the right synthetic fiber often involves comparing polypropylene with other common options like polyester and nylon. Each fiber has its own strengths and weaknesses, making them suitable for different purposes. Understanding these differences is key for procurement officers like Mark Thompson who need to balance performance and cost.
Here’s a comparative overview:
Feature | Polypropylene (PP) Yarn | Polyester Yarn | Nylon Yarn (Polyamide) |
---|---|---|---|
Density (g/cm³) | ~0.91 (Lightest) | ~1.38 | ~1.14 |
Moisture Absorption | Very Low (<0.1%) | Low (~0.4%) | Moderate (~4.0%) |
Tenacity (g/d) | Good to High (3.0 – 9.5) | High to Very High (3.0 – 9.5+) | Very High (4.0 – 9.0+) |
Abrasion Resistance | Good | Very Good | Excellent |
Chemical Resistance | Excellent (Acids, Alkalis) | Good (Resists most chemicals, solvents) | Good (Weakened by strong acids) |
UV Resistance | Fair (Requires Stabilizers) | Good to Excellent | Fair to Good (Requires Stabilizers) |
Melting Point | Lower (~165°C / 329°F) | Higher (~260°C / 500°F) | Higher (~220-265°C / 428-509°F) |
Dyeability | Difficult (Requires Dope Dyeing) | Good (Disperse Dyes) | Good (Acid Dyes) |
Elasticity / Stretch | Good Elasticity, Low Stretch | Moderate Elasticity, Good Recovery | High Elasticity, Excellent Recovery |
Cost | Generally Lower | Moderate | Generally Higher |
Key Takeaways from the Comparison:
- Weight: Polypropylene is the clear winner if lightweighting is the primary goal.
- Moisture: PP’s hydrophobic nature is superior for applications demanding quick drying and water repellency (sportswear, marine).
- Strength: Nylon often leads in tenacity and abrasion resistance, followed closely by polyester and high tenacity PP yarn.
- Chemicals: Polypropylene generally offers the broadest resistance to chemicals, especially acids and alkalis.
- Temperature: Polyester and Nylon have higher melting points, making them better suited for high-temperature applications.
- Color: Polyester and Nylon are easier to dye post-production, but dope dyed polypropylene offers excellent colorfastness.
- Cost: Polypropylene is often the most cost-effective option among the three synthetic materials.
The best choice depends entirely on the specific requirements of the end product. For cost-effective, lightweight, moisture-resistant applications with excellent chemical resilience, polypropylene yarn is often an unbeatable choice.
Why Choose Polypropylene Yarn for Your Textile Needs?
Selecting polypropylene yarn for your manufacturing or textile projects comes down to leveraging its distinct advantages. One of the most compelling reasons is its cost-effectiveness. Generally, PP yarn is less expensive to produce than other synthetic fibers like polyester or nylon, making it an economically attractive option, especially for large-volume applications like carpet backing, non-woven fabrics, and disposable goods. This allows businesses to manage production costs effectively while still creating durable products.
Beyond cost, the unique performance characteristics are a major draw. Its exceptionally low weight is a significant benefit in automotive, luggage, and apparel industries. The outstanding chemical resistance makes it indispensable for industrial filters, geotextiles, and lab wear. Furthermore, its low moisture absorption and quick-drying properties are highly valued in sportswear, marine applications (rope, nets), and hygiene products. This inherent hydrophobicity also contributes to its excellent stain resistance, a desirable trait for upholstery and floor coverings. The yarn is a lightweight yarn that packs a punch in performance.
Finally, the versatility of polypropylene yarn cannot be overstated. It can be engineered into various forms – fine filaments for soft fabrics, high tenacity yarn for demanding industrial tasks, fibrillated yarn for robust applications, and non-woven structures. It blends well with other fibers and can be manufactured with specific properties like UV resistance or flame retardancy. This adaptability, combined with its inherent strength, good elasticity, and resistance to biological attack (mold, mildew), makes polypropylene yarn a reliable and adaptable choice across the textile industry, industrial applications, and consumer goods manufacturing. Its ability to be dope dyed ensures vibrant, long-lasting colors are achievable, meeting aesthetic demands alongside functional requirements.
What Should You Look for When Sourcing Polypropylene Yarn from China?
For buyers like Mark Thompson, sourcing polypropylene yarn from China offers significant advantages in terms of cost and volume capacity. However, ensuring consistent quality and reliable supply requires careful consideration. Based on my experience as a manufacturer (Allen here!), communication and clear specifications are paramount. Clearly define your requirements: the type of yarn (filament, staple, fibrillated yarn), denier (thickness), tenacity (standard or high tenacity), color (dyed yarn specification, if applicable, mentioning dope dyed preference), UV stabilization needs, and packaging preferences (e.g., Cone polyproplene yarn). Providing detailed specs minimizes misunderstandings.
Quality consistency is often a key concern. Ask potential suppliers about their quality control procedures. How do they ensure consistency in tenacity, elongation, shrinkage, and color (if applicable) from batch to batch? Requesting samples for testing is standard practice. Don’t just rely on initial samples; inquire about their process for maintaining quality over long-term production runs. While certifications like OEKO-TEX might be less common for purely polypropylene yarn compared to polyester or cotton used in garment applications, inquire about any quality management system certifications (like ISO 9001) the factory holds. Understanding their manufacturing capabilities and the technology they employ (industrial production standards) is also crucial.
Finally, consider the supplier’s reliability and communication. Look for manufacturers with a proven track record and experience exporting to your region (USA, Europe, etc.). How responsive are their sales representatives? Efficient communication is vital to resolve any issues quickly and manage logistics effectively. Discuss lead times, shipping terms (FOB, CIF, etc.), and payment methods upfront. Visiting the factory or meeting representatives at textile exhibitions can build trust and provide valuable insights into their operations. Partnering with a reliable manufacturer ensures you receive high-quality polypropylene yarn consistently, avoiding potential pain points like shipment delays or specification discrepancies, and ultimately supporting your own production and profit goals.
Key Takeaways on Polypropylene Yarn:
- Lightweight Champion: Polypropylene yarn is the lightest synthetic fiber, offering advantages in weight-sensitive applications.
- Water Repellent: Its extremely low moisture absorption makes it quick-drying, stain-resistant, and ideal for wet conditions or activewear.
- Chemically Robust: Exhibits excellent chemical resistance, particularly against acids and alkalis, suitable for industrial use.
- Colorfast Solution: While difficult to dye traditionally, dope dyed polypropylene yarn provides excellent, long-lasting color integrated into the fiber.
- Strong & Versatile: Offers good to high tenacity, especially in specialized high tenacity yarn variants, making it suitable for ropes, nets, fabric, and geotextiles.
- Wide Applications: Used extensively in carpets, upholstery, automotive interiors, rope, non-woven fabrics, sportswear, and technical textiles.
- Outdoor Capable (with UV protection): Naturally resistant to moisture and mildew, but requires UV stabilizers for long-term sun exposure.
- Cost-Effective Choice: Often more economical than polyester or nylon, providing good performance value.
- Sourcing Smart: When sourcing (especially from China), prioritize clear specifications, quality control verification, reliable communication, and understanding the supplier’s capabilities.
Understanding these facets of polypropylene yarn empowers you to make better material choices for your textile and manufacturing needs.